Is Your Product Design Costing You More Than it Should?
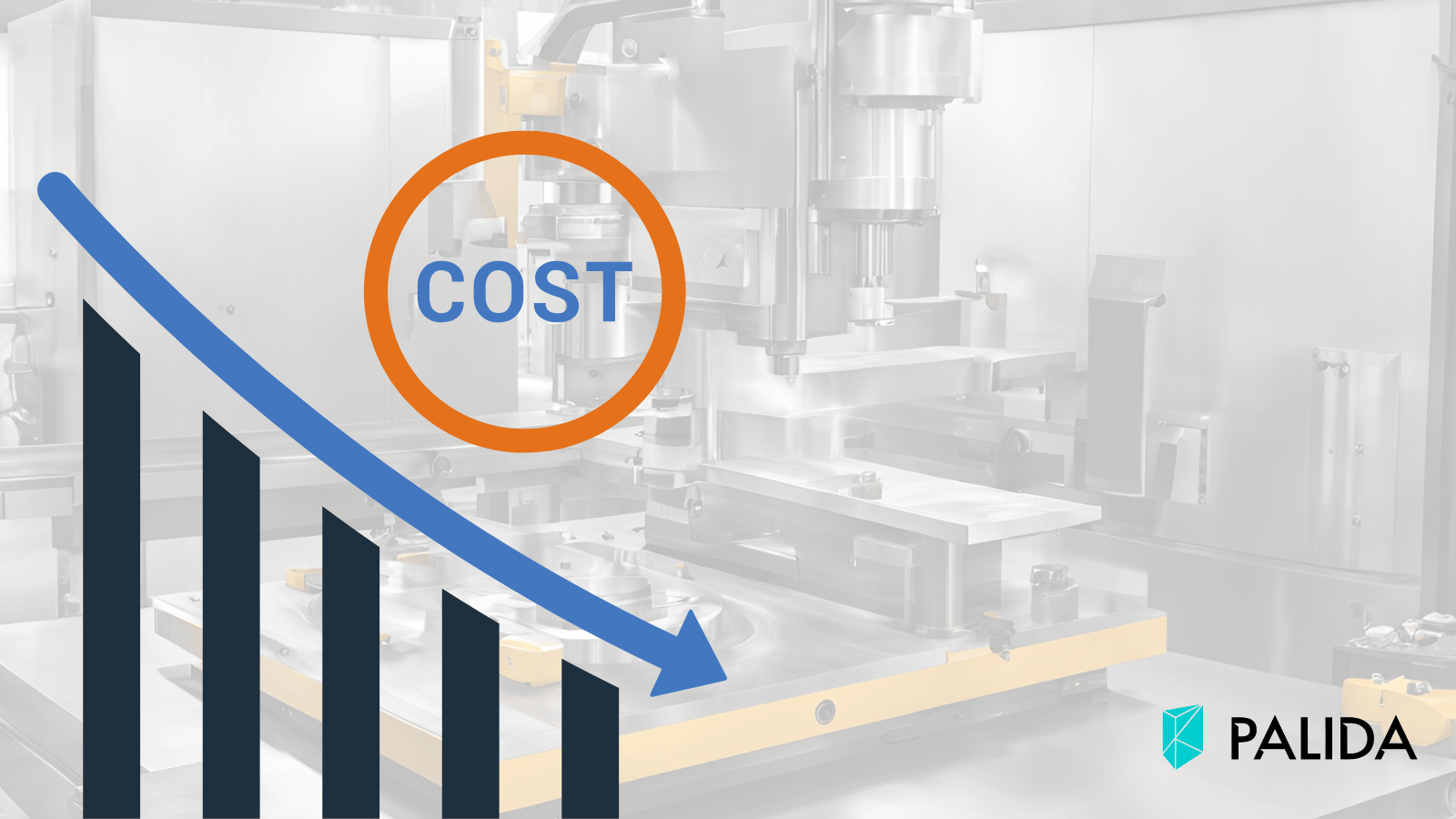
Ever wonder why some products just seem to flow through manufacturing while others hit snag after snag? The secret often lies in producibility - a design philosophy that prioritizes not just how well a product works, but how easily and affordably it can be made. It's about designing with the entire manufacturing process in mind, from the initial concept to the final assembly. Ready to dive in?
The Pillars of Producibility: It's More Than Just a Pretty Picture
Producibility isn't a single thing; it's a mindset built on several key principles:
- Keep it Simple, Seriously: Complex designs? They might look impressive on paper, but they often lead to increased costs across the board: manufacturing, maintenance, even repair.
- Materials Matter: The material you choose is a pivotal decision. It can make or break your manufacturing process.
- Tolerances: When Less is More: Tight tolerances and super-smooth surfaces may seem ideal, but they often require specialized and costly manufacturing.
- Flexibility is Your Friend: When you can adapt to different materials and processes, you're in a much better position for efficient production.
- Clarity is King: Make sure your design information is crystal clear. Ambiguity leads to errors and delays.
When Does Producibility Start? The Sooner, The Better!
The best time to think about producibility? As early as possible in the product design phase. Why? Because the design stage locks in a large percentage of production costs. Here's how producibility activities play out across the design phases:
- Concept Exploration: This is where you identify your technology, evaluate materials, and pinpoint any high-risk areas.
- Preliminary Design: At this stage, focus on figuring out which manufacturing processes are available, and the impact on your final product. Also, standardize your components as early as possible.
- Detail Design: Now, evaluate all your materials, manufacturing processes, testing methods, and finalize your plan for production.
- Production: This final phase is about ensuring that the actual production parts meet all the necessary requirements and work the way they should.
The Balancing Act: Trade Studies and Cost Drivers
To achieve the best design, you need to perform trade studies. Think of design as a triangle. You need to balance three key factors: time, cost, and performance. Target values should be established for engineering and production variables. This process helps find the best materials and processes for your design. Risk assessment is essential.
Need help with your design challenges?
Let's discuss how we can optimize your product for manufacturing.
Every manufacturing process has its own cost drivers, these can include:
- Machined Parts: Think about material type, amount of material removed, surface finish needs, and how tight your tolerances are.
- Forgings: The actual forging process and material quality are significant cost factors.
- Castings: Here, it's the casting process, material quality, and the complexity of your design that will affect cost.
- Sheet Metal: Material type, design complexity, and your production volume will all affect cost.
- Surface Treatment: Preparation, size and the materials used are key elements in this stage.
- Composites: Factors like fiber mix, resin, and part size drive the cost here.
- Electronics: Single source items, number of test points, and your tolerance requirements are key drivers.
Near-Net Shaping: Cutting Down on Finishing
Near-net shaping is another way to potentially lower costs. Instead of traditional methods, these processes create parts that are close to their final shape, minimizing the need for extensive finishing. Here are a few options:
- Precision Forging: Ideal for aluminum and magnesium, this technique is used to produce parts to greater accuracies.
- Investment Casting: Great for intricate shapes, this process works best for smaller parts with tight tolerances and high-strength alloys.
- Injection Molding: It's perfect for large-scale production of complex plastic parts.
- Powder Metallurgy: This method creates parts by compacting and sintering metal powder. It's good for complex parts, and unusual alloys.
Design for Assembly: Making it Easy to Put it All Together
Design for assembly (DFA) focuses on how to make a product easy to assemble. It's about thinking about assembly problems from the beginning. Key principles include:
- Multifunction Parts: Combine as many parts and functions as possible into single components.
- Standardization: Standardize parts and processes wherever you can.
- Self-Locating/Self-Fastening Features: Use features that make assembly easier, like tabs or snap-fit fingers.
- Component Orientation: Design parts to be symmetrical or asymmetrical in an obvious way, so they are easier to work with.
- Facilitate Insertion: Make assembly a smooth and easy process using guide surfaces and simple movements.
Assembly can be manual or automated, each with unique part design needs. When it comes to manual assembly, consider symmetry, weight, size, and shape of parts. Automated assembly requires attention to part symmetry, shape and stability.
Cost drivers of assembly include:
- Mechanically Fastened Assemblies: Consider accessibility, jigging, the materials being joined and the number of fasteners needed.
- Welding: The type of weld, the joint, the material, and the complexity of the path.
- Adhesive Bonding: The materials, the adhesive system, and the type of joint.
- Electronic Assembly: the type of connectors, soldering processes, and the amount of manual wiring.
Ready to Optimize Your Designs?
By focusing on producibility, you can create products that are not only functional and high quality, but also cost-effective and easier to manufacture. It's a win-win for everyone!
Ready to take the next step?
Our team is here to help you implement these producibility principles.